Un savoir-faire français ancestral
Le nom Emmanuelle Khanh concentre une histoire, la noblesse du travail de la main, cette identité française, dans le style et le savoir‐faire. La Maison choisit de promouvoir la production locale à travers un processus artisanal et une fabrication de haute qualité. Elle rend hommage à ses partenaires, qui façonnent chaque pièce à la main avec le plus grand soin. Au total, plus de 80 étapes sont nécessaires à la fabrication d’une paire de lunettes.
PREMIÈRE DÉCOUPE ET SÉCHAGE
Les montures Emmanuelle Khanh sont découpées dans l’acétate, une matière organique obtenue par la plastification de flocons de coton et de cellulose de bois. C’est une matière souple, vivante, qui offre des possibilités infinies de coloration et de motifs. Les feuilles d’acétate sont coupées en petits rectangles (labos), à la taille de la monture, qui sont séchés dans une étuve pour stabiliser la matière et la débarrasser des résidus de colle et de plastifiants.
COLLAGE DES TAQUETS
Pour l’usinage des plaquettes de nez “collées”, sur chaque labo est collé un taquet : un carré de matière cristal. Cela permet d’avoir une surépaisseur au niveau du nez, donc des plaquettes plus profondes et plus de confort.
DÉCOUPE ET GALBAGE DES FACES
Dans chaque rectangle de matière, une face de lunette est sculptée : cinq ou six fraises différentes viennent façonner la forme des yeux, le contours, et les éventuels biseaux intérieurs et extérieurs. La face est ensuite chauffée, ce qui rend la matière plus malléable, puis pressée contre un moule courbé pour lui donner son galbe.
SHOOTAGE DES CHARNIÈRES
À l’intérieur de rectangles d’acétate qui deviendront les branches, sont glissées les charnières soudées sur l’armature qui va donner son maintien et de la solidité à la monture. Elles sont injectées dans la matière, l’acétate étant rendue plus molle en son centre grâce à un fil chaud.
DÉCOUPE ET GRAVURE DES BRANCHES
Les labos de branches déjà shootées sont découpés suivant la forme d’un outillage en métal. Une fraise, reliée à un repère verticalement, vient découper l’acétate. Les branches sont ensuite gravées une à une au laser : à l’intérieur, les marquages indiquant la référence et les dimensions de la lunette ; à l’extérieur, l’emplacement
du logo.
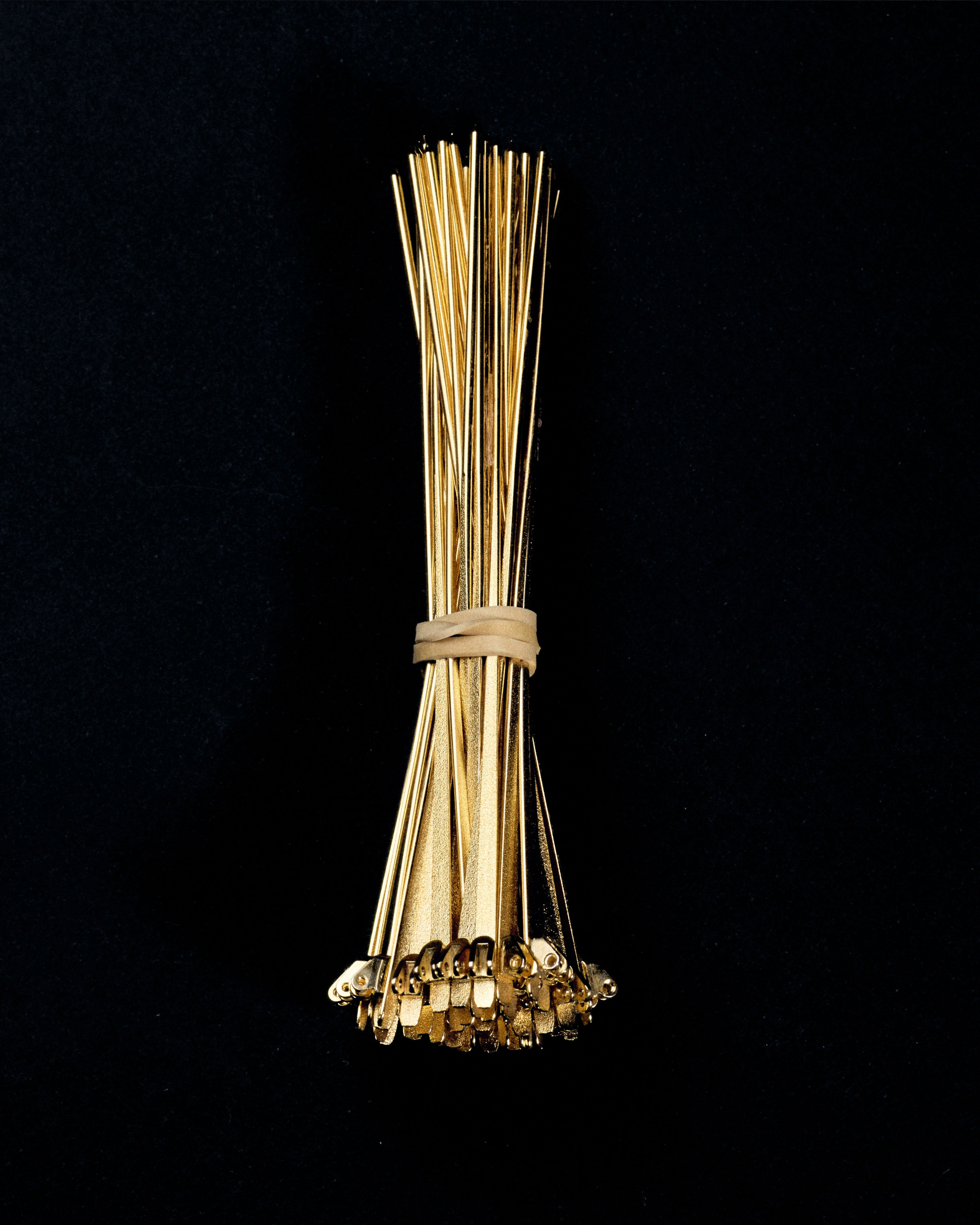
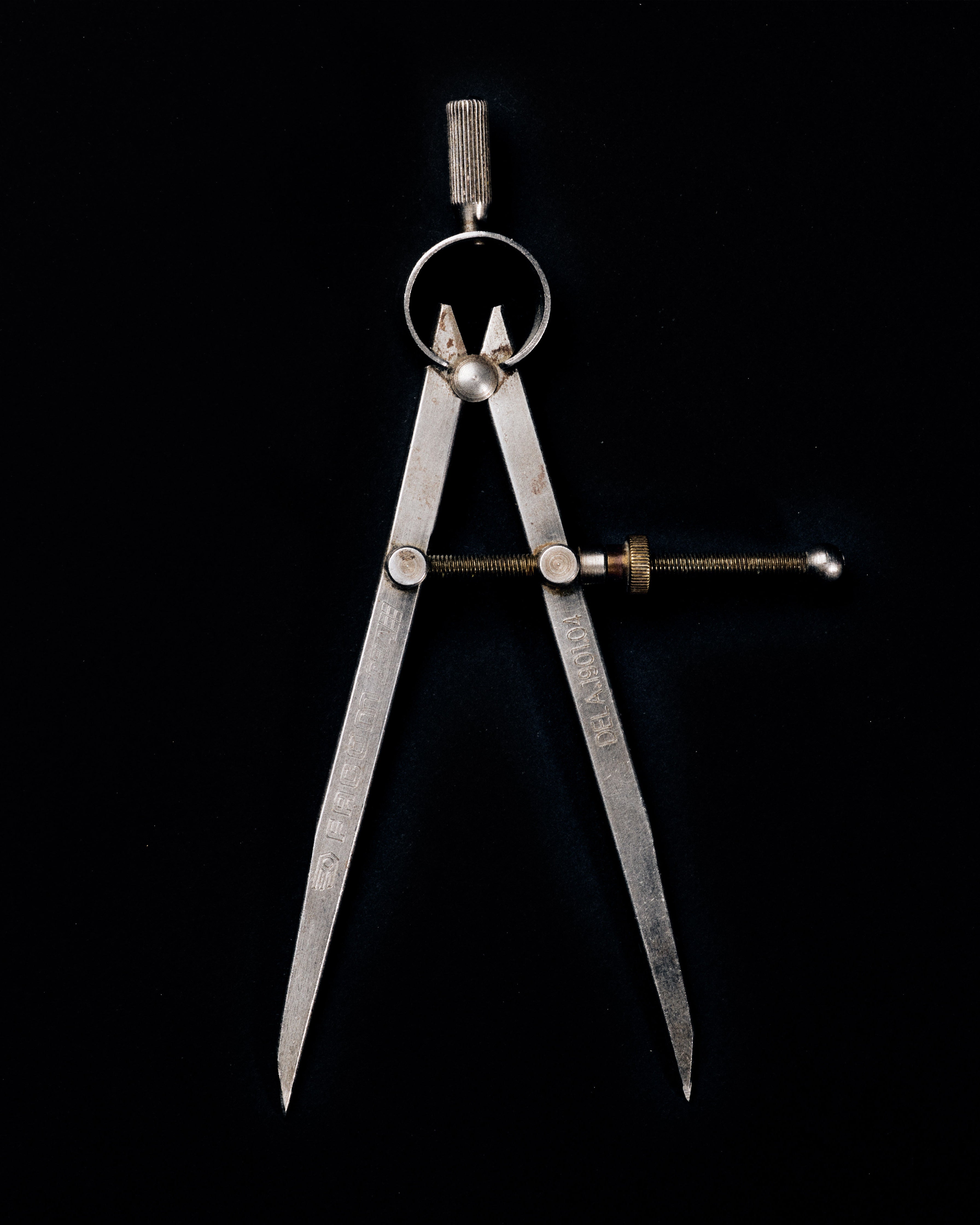
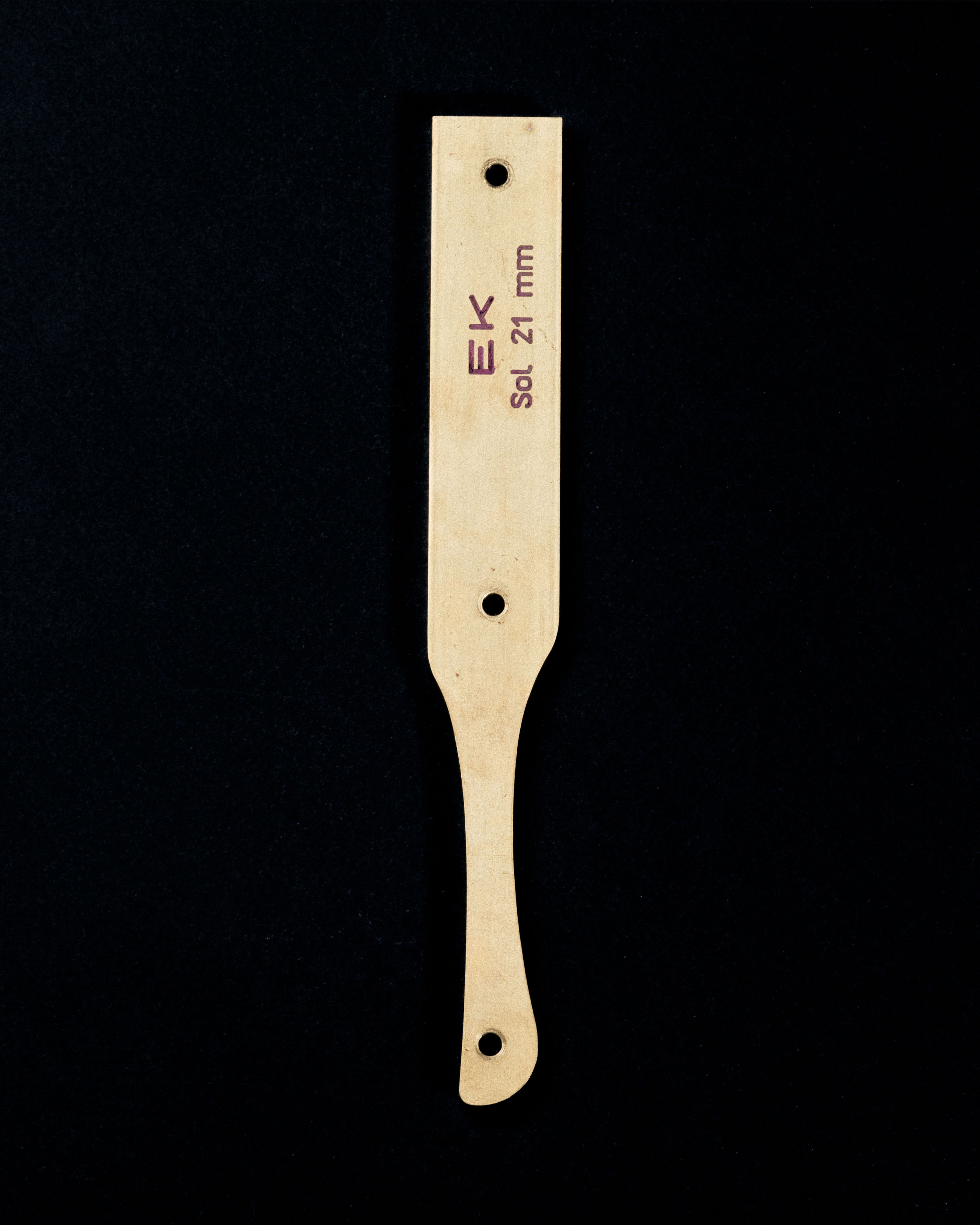
POSE DU LOGO SOUS RÉSINE & SPATULAGE
Sur chaque branche, les enjo EK sont déposées à la main, un par un à l’aide d’une pince, dans les incisions faites au laser. Elles sont ensuite recouvertes d’une résine
transparente. La résine doit sécher plusieurs heures avant d’être arasée. Les spatules des branches sont ensuite chauffées et courbées pour apporter du confort derrière l’oreille.
BAC À ULTRASONS
La face et les branches sont placées dans un bac à ultrasons. Les ultrasons éliminent les plus fins copeaux d’acétate dus aux différentes étapes de découpe.
POLISSAGE EN TONNEAU
La face et les branches sont déposées dans un tonneau
horizontal plein de copeaux de bois couverts de pâte à polir. Une fois fermé, il tourne pendant une semaine, au cours de laquelle les copeaux viennent doucement abraser et lisser la surface de l’acétate. Au préalable, les charnières métalliques sont recouvertes de cire pour éviter les rayures. Au cours de la semaine, les futures lunettes passent dans trois tonneaux différents, du plus fort au plus fin, et font plusieurs aller-retours dans les bacs à ultrasons. Au sortir des tonneaux, les pièces sont polies et brillantes.
MONTAGE DES BRANCHES ET ANGLAGE
Sur les branches sorties des tonneaux, les inscriptions gravées au laser sont remplies à la peinture dorée et les protections sur les charnières retirées une à une. La face et les branches sont ensuite assemblées, vissées à la main. Le raccord entre les branches ouvertes et la face est ajusté, ce qui peut dépasser est limé pour que le tenon entre les branches et la face soit lisse au touché et au regard.
POLISSAGE FINAL
La lunette est une dernière fois polie à l’aide d’une roue duveteuse tournant à une vitesse importante. Cette dernière étape permet de dépoussiérer la lunette des éventuels copeaux créés lors du raccord des branches, et de faire disparaître les micro-rayures qui ne seraient pas parties aux tonneaux.
DÉCOUPE ET MONTAGE DES VERRES
Les verres sont découpés seulement une fois la lunette polie, pour s’adapter parfaitement à la forme finale de l'œil. Chaque paire de verres est minutieusement placée dans une découpe. La pression ne doit être ni trop forte, pour ne pas casser le verre, ni pas assez, pour le couper de façon nette. Les verres sont montés sur la lunette assemblée. La monture est enfin complète.